Dans tous les types d'industrie, les personnes peuvent être exposées à des départs de feu ou à des gaz toxiques. Détecter les flammes et les fuites pour se prémunir contre les accidents est le souci majeur de tous les responsables de site...
Raffineries, centrales nucléaire, plates-formes de forage, chaufferies, parkings, dépôt de carburants, de gaz ou de produits chimiques sont autant de sites où le moindre départ de feu peut avoir des conséquences humaines, environnementales et matérielles dramatiques. C’est pourquoi la détection incendie est l’une des préoccupations majeures des différents intervenants dans le domaine de la protection incendie au sein des industries ou sites à hauts risques.
Les détecteurs de flamme
La mise en place de détecteurs de flamme est particulièrement adaptée aux grandes aires de stockage où le risque d’élévation rapide de la température est élevé. Ce moyen de détection est plus particulièrement adapté à la détection des feux de gaz et de liquides exempts de fumée. Le stockage de quantités importantes de produits inflammables, la configuration particulière des lieux où des conditions de températures singulières amènent à préférer ce type de détection dont la rapidité d’action présente l’avantage de travailler dans des environnements exigeants. Les flammes sont constituées de particules et de gaz, qui, portés à une température élevée, émettent un rayonnement. Une analyse de la puissance de ces rayonnements par les capteurs équipant les détecteurs de flammes révèle deux spectres, un visible proche de l’infrarouge (IR) et l’autre concernant les ultraviolets (UV).
Les appareils les plus performants disposent d’une combinaison des deux types de capteurs. Il arrive cependant que la détection des flammes soit perturbée, voire difficile, du fait des rayonnements venant interférer avec le spectre du feu, comme celle de la lumière naturelle ou ambiante, la fiabilité du système dépend alors de la qualité du détecteur choisi.
• La détection de flamme UV
Les détecteurs de flamme UV sont sensibles aux rayonnements UV émis par l’éclairage direct de certaines sources lumineuses comme les lampes au mercure ou au xénon, ou encore aux arcs produits lors de travaux de soudure (dans ce dernier cas, il est conseillé de neutraliser la zone concernée pendant la période où ont lieu les travaux). Pareillement, ils sont tout aussi vulnérables aux sources de rayonnement gamma et X non masquées, aux rayonnements UV émis par les éclairs lors d’un orage et aux atmosphères poussiéreuses, brumeuses ou enfumées.
• La détection de flamme IR
Souvent équipés de cellules au silicium ou au sulfure de plomb, les détecteurs infrarouge sont les détecteurs de flamme les plus utilisés du fait de leur coût et de leur facilité d’utilisation. Ils permettent une détection au travers des fumées et sont efficaces pour les feux d’hydrocarbures (liquides, gaz ou solides). Leurs performances sont aussi notables sur des mauvais taux de combustion. En revanche, ils sont sensibles à la présence d’eau et sont peu performants sur les combustions très vives (gaz de méthane, acétylène, GPL…). Les barrières infrarouge agissent schématiquement comme des cellules photoélectriques qui détectent et mesurent le passage du gaz dans leur faisceau. Les ensembles sont constitués d’un émetteur et d’un récepteur placé à distance. L’unité de mesure est exprimée en partie par million (ppm) mètre ou / et en limite inférieure d’explosivité (LIE) mètre.
La détection des gaz
Dans tous les types d’industries, les personnes peuvent être exposées à de nombreux gaz toxiques. Détecter les fuites et se prémunir contre les accidents est le souci majeur de tous les responsables de site. Qu’est-ce qu’une atmosphère explosible ? Selon la directive, une atmosphère explosible est constituée d’un mélange d’air et de substances inflammables sous forme de gaz, vapeurs, brouillards ou poussières, dans lequel, après inflammation, la combustion se propage à l’ensemble du mélange non brûlé selon la concentration et le confinement.
La protection des sites pétroliers et gaziers fait l’objet d’une attention toute particulière des services de sécurité, de contrôle et de prévention d’autant plus lorsqu’ils sont situés à proximité des agglomérations. Pour les sites pétroliers, la détection des gaz et vapeurs d’hydrocarbures se fait plus particulièrement à l’aide de détecteurs explosimètres à perles catalytiques. Une étude technique préalable définit les zones à risques et l’emplacement de chaque détecteur. Ces derniers sont alors raccordés à une centrale de détection qui gère les asservissements tels que feu à éclats, sirène, coupure électrique, etc. Les dépôts gaziers (gaz propane et butane liquides) sont majoritairement équipés de détecteurs de gaz à technologie catalytique ou infrarouge et de détecteurs de flamme. Difficultés d’accès, températures élevées, présence de poussière, présence de basse ou haute pression sont autant de conditions dans lesquelles il est impossible d’installer des capteurs à proximité des risques potentiels de fuite. Aussi, certains fabricants ont développé une variété d’accessoires permettant d’obtenir une détection fiable avec un minimum de maintenance.
Les zones à risques sont déterminées de la façon suivante :
• Zone 0 : Atmosphère explosive en permanence
Zone dans laquelle un mélange explosif de gaz, de vapeurs ou de poussières est présent en permanence.
• Zone 1 : Atmosphère explosive souvent présente
Zone dans laquelle un mélange explosif de gaz, de vapeurs ou de poussières est susceptible de se former en service normal de l’installation.
• Zone 2 : Atmosphère explosive accidentellement présente
Zone dans laquelle un mélange explosif de gaz, de vapeurs ou de poussières ne peut apparaître qu’en cas de fonctionnement anormal de l’installation.
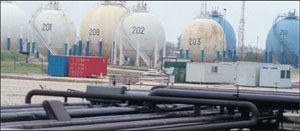
La détection H2S
Le principe de cette détection est basée sur la propriété qu’a l’hydrogène sulfuré de s’absorber sur un oxyde métallique (MO), semi-conducteur film mince très spécifique. Il s’agit d’une absorption physique, donc réversible. Ne s’agissant pas d’une absorption chimique, il n’y a ni « usure », ni « consommation » de la partie sensible. Jusqu’en 1973, le marché de la détection H2S était assez restreint. En effet, les cellules électrochimiques, dont le principe et le développement dataient de 1905, ne permettaient pas à cause de leur fragilité, des interférents et de leur grande dépendance vis-à-vis des conditions climatiques (température, pression et humidité) de répondre aux besoins des applications pétrolières extérieures à environnements délicats.
C’est avec le développement du semi-conducteur General Monitors spécifique à l’H2S (seul le méthyl mercaptan interfère à 10 %) que le marché mondial de la détection H2S s’est développé sur les plates-formes offshore et onshore de forage et de production, dans les usines de traitements de gaz et dans le raffinage. Jean-Claude Toelen, de la société Autochim, ajoute que, dans le domaine de la détection incendie, tous les détecteurs ne sont pas incompatibles entre eux et sont même souvent utilisés en complément les uns des autres.
La mesure des gaz toxiques
De nos jours, l’évolution des techniques et des matériels disponibles sur le marché permet de mesurer directement sur site les concentrations de gaz toxiques et de calculer leurs VLE (Valeurs Limites d’Exposition) et leurs VME (Valeurs Moyenne d’Exposition). C’est le cas pour la détection par photoionisation, du principe de la cellule électrochimique et de la spectroscopie photoacoustique.
De leur côté, les détecteurs de gaz multiples peuvent déceler, en continu et simultanément, jusqu’à cinq substances dangereuses.
Détecteurs combustibles catalytiques et ultrasons
Le principe des détecteurs combustibles catalytiques est basé sur l’oxydation des gaz ou des vapeurs à détecter. Une source de courant autorégulé est fournie sur un montage en pont de Wheatstone contenant un filament de platine chauffé. Les modèles les plus récents, dits à bille catalytique, fonctionnent grâce à un filament de platine enroulé et noyé dans une bille de céramique poreuse.
Une branche du pont est constituée par le détecteur comprenant deux billes catalytiques. L’autre branche contient un diviseur à résistance. Les deux perles catalytiques « active » et de « référence » sont rigoureusement identiques. Lorsqu’un mélange composé de gaz combustible et d’air est diffusé dans le détecteur à travers le pare-flamme, une oxydation catalytique proportionnelle à la concentration de gaz combustible de ce mélange se produit uniquement sur la perle active. La réaction exothermique qui en découle modifie la résistance de cette perle entraînant un déséquilibre de tension sur le pont.
En s’échappant de son point de fuite, le gaz génère des ultrasons qui résultent de son échappement à la vitesse du son. Le microphone utilisé comme capteur détecte alors ces ultrasons et dirige le signal vers un filtre spécialement conçu pour ne laisser passer vers le circuit de délai d’alerte que le bruit compris dans le spectre fréquentiel ultrasonique. Par ce principe, le détecteur n’a plus besoin d’être en contact direct avec la fuite.
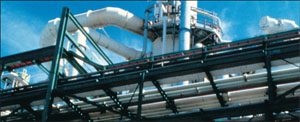
Les normes
Beaucoup de sites industriels présentent des risques pour les personnes, l’environnement et les équipements et, à ce titre, répondent à des normes spécifiques selon leur niveau de dangerosité.
C’est le cas pour les normes EN 61511 et EN 61508 concernant les systèmes industriels et les équipements électriques ou électroniques qui leur sont associés et assurant un haut niveau de fiabilité des équipements.
• La norme EN 61508 s’adresse aux concepteurs de dispositifs pour les produits incluant une fonction instrumentée de sécurité (SIF) réalisée à partir de capteurs et d’actionneurs gérés par un automate programmable industriel (API) ou un système de commande réparti. Cette norme englobe, par ailleurs, les aspects hypothétiques, comme la possible défaillance des composants et les éventuelles erreurs de conception. Elle présente une approche générale de toutes les fonctions relatives au cycle de vie de sécurité de systèmes électriques ou électroniques programmables ou non (E/E/PES) utilisés pour réaliser des fonctions de sécurité.
• La norme EN 61511 s’adresse particulièrement aux concepteurs des systèmes. Elle met à la disposition des clients finaux et des intégrateurs des méthodologies qui aident à réduire les risques tout en permettant un compromis entre la sécurité et la disponibilité des installations.
• La norme NFS 61950 précise les exigences requises pour les matériels de détection d’incendie, tableaux de signalisation et organes intermédiaires. La règle Apsad R7 spécifie les conditions d’utilisation et les règles d’installation des détecteurs d’incendie.
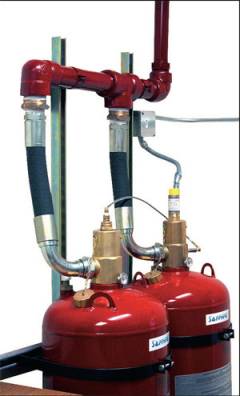
Zoom sur : Industrie agroalimentaire, l’ammoniac un fluide friorigène à surveiller
L’entretien des installations faisant appel à l’ammoniac comme fluide de refroidissement fait l’objet d’une attention toute particulière.
En effet, certains équipements vieillissant ou soumis à des vibrations peuvent faire apparaître des défauts notamment au niveau de joints. Les risques d’explosion sont alors bien présents.
Ainsi, l’arrêté du 16 juillet 1997 (art. 42) relatif aux installations de réfrigération employant l’ammoniac stipule clairement les obligations et les conditions d’installation des systèmes de détection, des alarmes qui y sont liées et des asservissements des ventilations additionnelles éventuelles.
D’autre part, l’arrêté du 23 février 1998 définit les installations classées soumises à déclaration, liées à l’emploi ou au stockage de l’ammoniac.
Zoom sur : LES DIRECTIVES ATEX
Entrées en vigueur le 1er juillet 2003, les directives Atex (ATmosphères EXplosibles) imposent de nouvelles prescriptions aux fabricants et aux utilisateurs d’équipements pour zones à risque d’explosion.
La première de ces directives indique les exigences minimales concernant la sécurité des travailleurs amenés à travailler dans des atmosphères explosibles.
La seconde, la directive 94/9/CE, concerne la mise sur le marché des appareils et systèmes de protection destinés à être utilisés en atmosphères explosibles. Cette dernière est une directive dite nouvelle approche qui a pour objectif de définir des exigences essentielles afin de permettre la mise sur le marché des matériels.
Ainsi, seuls les produits correspondant aux exigences de cette directive peuvent être commercialisés dans les pays de l’Union européenne.
Elle prévoit notamment :
> l’agrément par un organisme notifié non seulement du produit (par examen CE de type), mais également l’agrément du système d’assurance qualité de production de son fabricant.
> l’apposition du marquage CE sur les étiquettes des différents produits.
> la distinction entre les atmosphères explosives dues à la présence de gaz, vapeurs ou brouillard et les atmosphères explosives dues à la présence de mélanges d’air avec des poussières.
> l’introduction de règles de conception et de fabrication visant à maximiser la sécurité des appareils, pour qu’ils puissent fonctionner de façon sûre pendant leur durée de vie prévisible.
En savoir plus
Cet article est extrait du Magazine APS – numéro 159 de mars 2007.
Pour plus d’information sur nos publications, contactez Juliette Bonk .
Commentez