Difficile d'être mal chaussé en termes d'équipement de protection individuel. Les fabricants redoublent d'effort pour améliorer la sécurité et le confort en gardant des coûts de production raisonnables.
Pour travailler, il est agréable de porter des chaussures de sécurité confortables et légères. Ces dernières années, les entreprises françaises ont beaucoup travaillé sur le squelette de la chaussure pour faire évoluer sa construction. Cet équipement de protection individuel (EPI) devient plus ergonomique tout en restant accessible financièrement. « Une tige classique pouvait comporter une centaine d’éléments. Aujourd’hui, nous nous inspirons des grandes innovations développées par les marques de sport et d’outdoor pour réduire la complexité de nos modèles. En utilisant les matières type microfibres, nous améliorons l’ergonomie et le confort pour les porteurs grâce, par exemple, à la réduction du nombre de coutures pouvant générer des frottements au niveau de la tige. Les rebuts matières sont également réduits, ce qui limite l’impact environnemental de la production », explique Laurent Rebstock, manager produit et marketing chez Uvex-Heckel, entreprise basée à La Walck (67). Heckel RUN-R et Uvex-1, les deux nouvelles gammes du fabricant dont le chiffre d’affaires s’élève à 260 millions d’euros, proposent des modèles en tige microfibre sans couture ainsi que de nouvelles semelles en polyuréthane améliorant le maintien de la voûte plantaire. Le cuir contre l’humidité. Certains matériaux sont incontournables dans la fabrication de cet équipement de protection individuel, comme le cuir. Sur un peu plus de 3,3 millions de paires de chaussures de sécurité produites par une vingtaine d’entreprises en France, « plus de 90% de la production concernent des chaussures de sécurité à dessus de cuir », souligne Dorval Ligonnière, responsable étude et marketing de la Fédération française de la chaussure. Ses nombreuses qualités n’ont pas encore trouvé d’équivalent dans les matériaux synthétiques. « Le cuir a des propriétés de résistance à l’eau et de résistance mécanique, difficiles à égaler, à coût équivalent, par rapport aux matières synthétiques », rappelle Laurent Rebstock. Le cuir, c’est aussi la respiration du pied. « Par jour, le pied d’une personne, en activité normale, transpire l’équivalent d’un verre d’eau. Cette eau doit s’évacuer car un pied humide est sensible au frottement, au froid et génère beaucoup d’inconfort. » Un des sites de production d’Uvex-Heckel basé en Italie est équipé d’un climatesteur. Il a été élaboré avec une école d’ingénierie en Italie. « Grâce à des simulations de sudation artificielle, on peut effectuer différentes mesures de capteurs et de pesage sur différentes zones du pied et constater l’efficacité des produits », explique Laurent Rebstock.
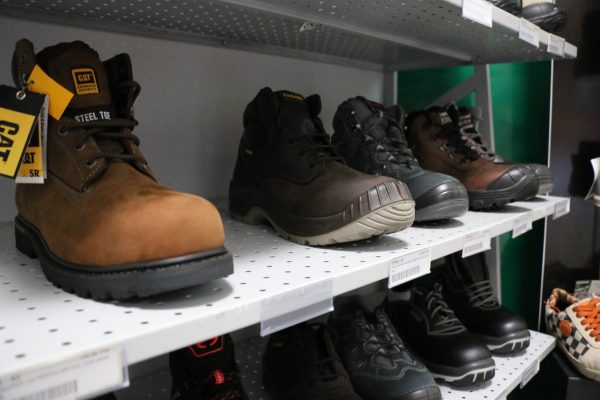
Un matériau coûteux difficile à remplacer. Incontournable dans le BTP, les gros œuvres et l’industrie lourd, le cuir commence cependant à être décrié. « Cela reste un produit avec une mauvaise image à cause de la pollution que sa fabrication engendre ainsi que la forte consommation en eau », souligne Nicolas Mille, président de Mille SAS basée à Courthézon (84) Depuis 2012, il constate que la qualité baisse alors que les problèmes d’approvisionnement se multiplient. « Aujourd’hui est le cuir devient un matériau coûteux. Son prix a augmenté de 20 %. C’est 20 % voire 30 % du prix de revient d’une paire de chaussures ». Sa fabrique de chaussures de sécurité, créée en 1912, travaille constamment sur de nouvelles conceptions de modèles afin d’améliorer la découpe du cuir et diminuer les chutes.Des chaussures lavables en machine. Gaston Mille, dont le chiffre d’affaires s’élève à 9,56 millions d’euros, modernise également ses gammes en utilisant de nouvelles matières et notamment la microfibre. Ainsi, le modèle Alma blanc (EN ISO 20347) a été créé pour répondre aux besoins des milieux hospitaliers : grâce à sa tige en microfibre, ce sabot antiglisse est également lavable en machine à 30°C et adapté aux conditions d’hygiène stricte. Gaston Mille a aussi élaboré le modèle Millenium Pied Protect, dont le brevet a été déposé. Cette sur-chaussure de protection se fixe aux souliers des visiteurs. Constituée de thermoplastique polyuréthane, cette protection est lavable à l’eau et peut être réutilisée par des personnes de différentes pointures. Le modèle est proposé en trois tailles uniques : S (35-38), M (39-44) et L (45-48) et possède un embout 200J en acier.
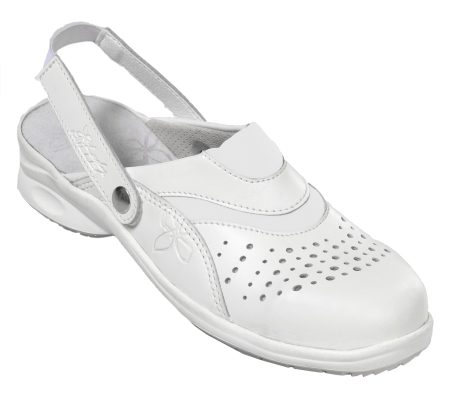
Apparition du non-métallique. Ces embouts sont l’un des composants les plus importants de la chaussure de sécurité. Ils sont garants de la bonne protection d’un pied. Pour Vincent Bia, co-gérant avec son frère de l’entreprise Bia située à Calais (62), « la grande révolution de ces dernières années, c’est l’apparition et l’omniprésence du non-métallique ». Travaillant depuis 1994 dans cette entreprise spécialisée dans la vente de fournitures industrielles et d’équipements de protection individuels, il a vu le marché évoluer. Les embouts composites ont peu à peu remplacé ceux en acier. Laurent Rebstock confirme la tendance : « On a développé le système Uvex Xenova, une technologie d’embout non-métallique qui protège autant tout en apportant légèreté et réduction des ponts thermiques. » Des analyses d’instituts ont validé des hauteurs résiduelles nettement plus élevées que les exigences de la norme EN 12568 lors du test de résistance à 200 Joules, une résistance à la pression nettement supérieure à cette même norme ainsi que des valeurs supérieures à la norme 12568 acier et aluminium. Dans la même tendance, de moins en moins de chaussures ont des semelles anti-perforation métalliques. Cela représente un gain de poids et aussi de souplesse. Toutefois, quelques professions ne peuvent pas s’en passer, comme dans le BTP. « Certaines utilisations préconisent de garder les semelles métalliques, notamment pour se protéger des pénétrations latérales », précise Vincent Bia.
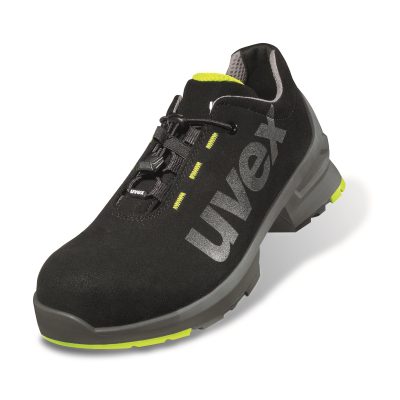
Le design, un critère de choix. En plus de la sécurité, l’évolution du design reste l’un des grands axes de développement des fabricants de chaussures. Selon les estimations de la Fédération française de la chaussure, la consommation apparente Française oscille entre 8 et 10 millions de paires au cours de ces dernières années. L’enjeu est alors de répondre aux différents besoins des travailleurs. « Les coquilles composites sont plus larges que les métalliques donc esthétiquement parlant les gens ont plus de mal à garder les chaussures en ville. Il est plus difficile de fabriquer des chaussures effilées, comme des escarpins », note Vincent Bia, dont l’entrepôt de 2.000 m² contient 4.000 paires de chaussures de sécurité . « La population jeune est plus exigeante sur le marché du travail. Ils ont plus la volonté de s’équiper à partir d’un équipement de sécurité basé sur un modèle de type basket ou converse. », poursuit-il. « Aujourd’hui, les innovations sont avant tout « la carte de visite » des fabricants. Il n’y a pas véritablement de révolution, c’est un marché assez stable. »
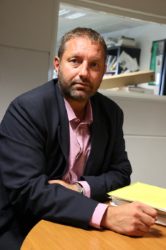
Bien s’informer pour s’équiper. Chez Bia, dont le chiffre d’affaires s’élève à 4,9 millions d’euros, 18 % des ventes de chaussures se font sur la chaussure noire S1P. « Le produit d’appel (le S1P) démarre aux environs de 16 euros. Les prix des paires de chaussures de sécurité peuvent atteindre les 150 à 200 euros pour des produits très spécifiques », précise Vincent Bia. Chez Modyf, entreprise spécialisée dans l’habillement professionnel basée à Erstein (67), le S1P est aussi un modèle très apprécié par les artisans. « Avec les nouveaux designs, on sort de la chaussure de sécurité traditionnelle lourde. Il y a un amalgame pour la clientèle qui se dirige vers un look plus léger plus confortable alors qu’inadapté à leur activité qui se révèle parfois trop « difficile » pour des modèles S1P. On essaye de les éduquer en les orientant vers des types de chaussures de sécurité conformes à leur besoin », explique Martin Wansart, chef de produit. Le comportement des clients varie aussi en fonction des activités. « Notre clientèle, surtout artisans et PME, investit beaucoup dans la qualité et le confort tandis que les grandes entreprises sont plus regardantes au niveau du prix. » La gamme de l’entreprise contient 60 modèles et les collections sont renouvelées chaque année.
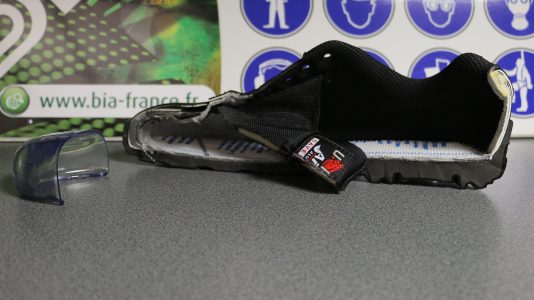
Des collections qui se renouvellent chaque année. Pour répondre aux attentes de l’artisan comme à celles de l’industriel aux 500 collaborateurs, le marché de la chaussure de sécurité s’inspire de plus en plus de la mode. « Maintenant, on ne s’aperçoit plus que les gens portent des chaussures de sécurité dans la rue. J’ai même des amis qui les gardent aux pieds après le travail car elles sont confortables, esthétiques, souples et légères. Les porter n’est plus une contrainte ! », souligne Vincent Bia. «Depuis deux ans, Lemaitre propose même de « tuner » la chaussure avec différentes couleurs. » Un souci du détail qu’on retrouve dans les magazines des fabricants qui utilisent de plus en plus souvent les méthodes de communication des marques de prêt-à-porter. Dans certaines pages, les clients posent avec les équipements de protection individuels. Le luxe fait aussi son apparition. En plus d’être fait d’un cuir noble, les chaussures sont vendues avec trois semelles d’épaisseurs différentes pour s’adapter à la morphologie du pied et un sac en plastique solide et « design » pour le transport. Et la gamme de tailles s’élargit. Il y a quelques années, les pointures proposées allaient du 38 au 48. Dorénavant, Bia fournit des chaussures de sécurité allant du 35 au 51.
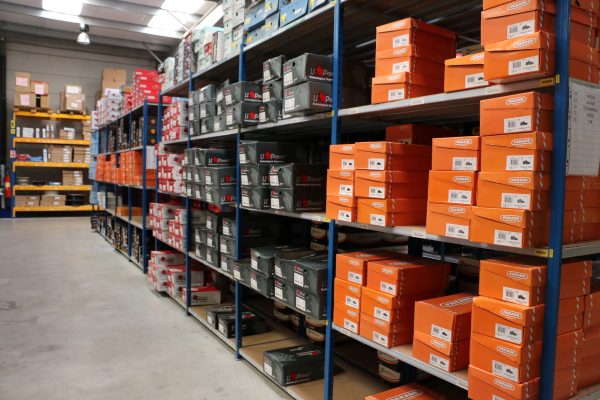
Des chaussures adaptées à la morphologie du pied. « La chaussure de sécurité devient pratiquement « orthopédique » : il faut du maintien, de la sécurité, du confort », analyse Nicolas Mille qui considère qu’elle devient aussi « un produit de consommation de masse, très coûteux et qui demande beaucoup de temps et de modifications ». Dans ce contexte, Gaston Mille a créé les gammes Flowergrip, New 1000 et Air 1000 avec des modèles de chaussures spécialement adaptés aux pieds féminins. Pour l’entreprise, l’amélioration constante des produits est très importante. Après mise sur le marché d’une collection, les utilisateurs font remonter les défauts et le fabricant améliore le produit. Bien que cela soit un travail constant, c’est aussi un avantage certain lorsque le modèle n’est pas le fruit d’une importation. En moyenne, deux mois suffisent pour le modifier. Une innovation représente six mois de travail et un an pour la lancer. Certains développements prennent plus de temps. « Le moule d’injection coûte cher, on le change tous les cinq ans », souligne Nicolas Mille dont l’entreprise propose 160 références de chaussures de sécurité déclinées en plusieurs niveaux de sécurité.

Actuellement, une vingtaine de fabricants français produisent des chaussures. Parmi elles, il y a Baudou SAS, Etche Sécurité, Jallatte-Jal Group, Rouchette, Sécurité 24, Nabad-Swedi, Richard Pontvert-Parachoc, Eram-Parade, Audouin, Solidur, Lemaitre, Heckel-Uvex, Beal-Sperian, Ets Boche, Annic MTS, Mille SAS, Bacou-Sperian, Le Chameau-Groupe Lafuma, Mardon, Argueyrolles-Noël Entreprises. Selon Dorval Ligonnière, responsable étude et marketing de la Fédération française de la chaussure, « tous les indicateurs montrent les difficultés rencontrées par les acteurs de l’univers du B2B. Toutefois, les industriels français de la chaussure de sécurité positionnés sur des niches de produits arrivent à maintenir leur activité, après, il est vrai, un net décrochage en 2009. » Les fabricants de chaussures de sécurité résistent à la concurrence internationale en « se positionnant sur des produits à forte valeur ajoutée où l’innovation et la recherche jouent un rôle important. »
Elodie Armand
L’avis de Jean-Pierre Boutonnet, chef de ventes chez Lemaitre Sécurité et président de la commission « Chaussures de sécurité » au Synamap (Syndicat national des acteurs du marché de la prévention et de la protection) dont les membres représentent 50% du marché français de la chaussure :
« Les utilisateurs sont en attente de produits lookés, légers, confortables, résistants et sûrs. Pour répondre à ce besoin, les fabricants de chaussures de sécurité sont confrontés à des problématiques complexes, comme celle de concevoir des produits toujours plus légers, répondant toutefois aux exigences de la norme. Pour atteindre cet objectif, les semelles injectées en polyuréthane double densité sont majoritairement utilisées, ce matériau étant plus léger que le caoutchouc. A l’intérieur des chaussures, les embouts non-métalliques et semelles anti-perforation en fibres textile haute-ténacité sont de plus en plus demandés car ils permettent d’être conformes à la norme NF EN ISO 20345, tout en étant plus souples et confortables. A Par ailleurs, ils protègent mieux du froid et ne sont pas détectables aux portiques de sécurité, ce qui intéresse certains milieux comme les aéroports ou la logistique. Néanmoins, les embouts en matériaux non métalliques sont souvent plus volumineux que leurs homologues en acier. Ce qui pose parfois des problèmes esthétiques et paradoxalement de poids. En alternative certains fabricants proposent des embouts en aluminium, un métal toutefois plus onéreux que l’acier. Il est a noté que les inserts anti-perforation en acier inoxydable protègent mieux contre les pointes de petit diamètre que les inserts en fibres haute-ténacité.»
Propos recueillis par Eliane Kan
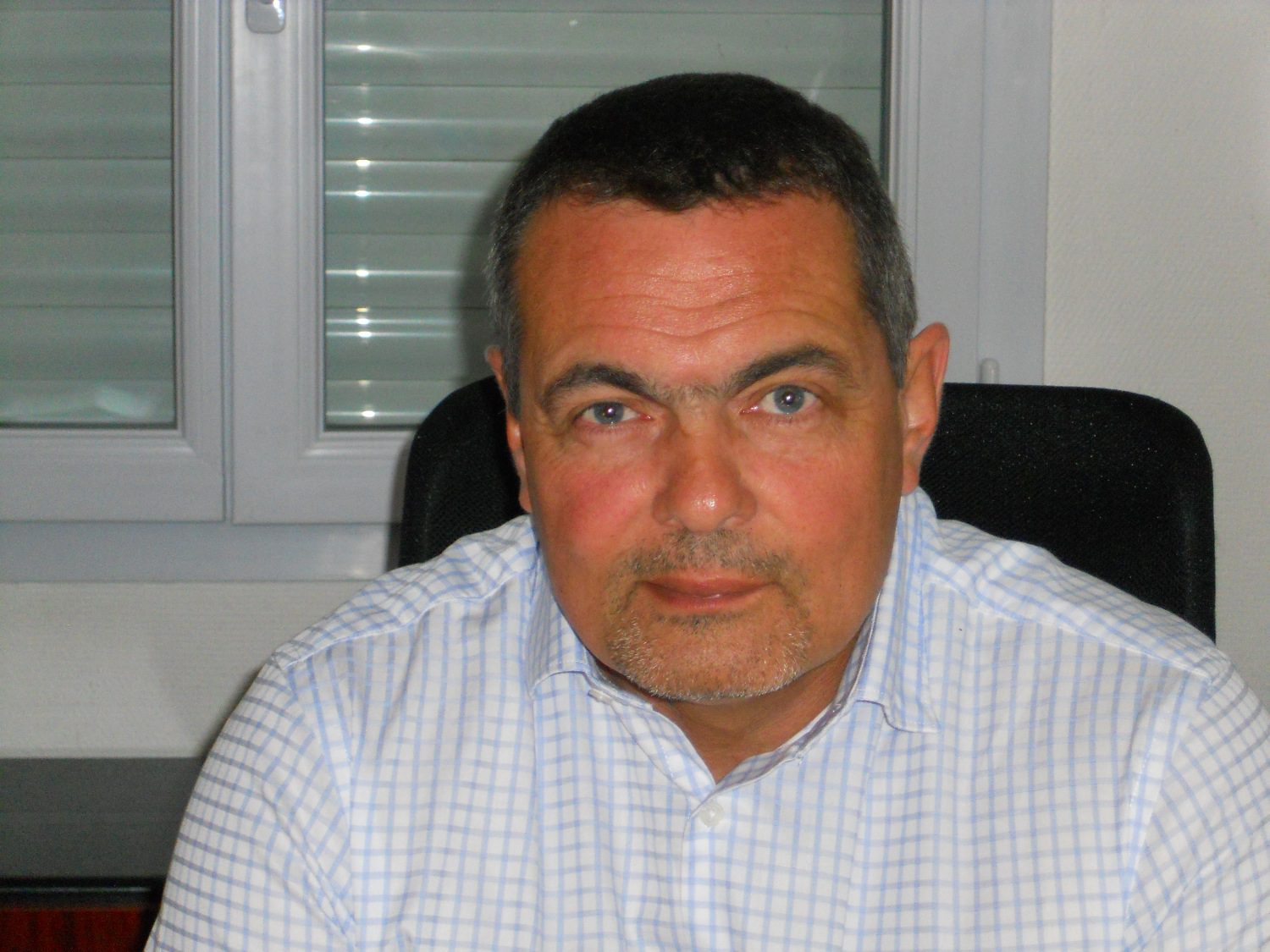
commission « Chaussures de sécurité »
au Synamap. ©DR
Commentez