Dans des usines automobiles, de hautes cadences soumettent les salariés à une augmentation des risques mécaniques. Glissades, chutes, blessures et TMS mais également risques liés aux machines sont en augmentation depuis un an dans ce secteur... qui ne déclare pas toujours les accidents de travail de ses employés.
En France, près de 129 000 salariés travaillent à la fabrication de plus de 5,5 millions de véhicules automobiles par an. En 2010, selon la Caisse nationale d’assurance maladie (CNAMTS), 1 % d’entre eux (1 270 personnes) a fait l’objet d’un accident sur leur lieu travail, à savoir l’usine de construction automobile. Un phénomène en hausse par rapport à 2009 (+ 6,7 %). Pour tenter d’inverser la vapeur, les constructeurs multiplient les initiatives. « Nos ingénieurs intègrent la sécurité des employés dès la conception des véhicules », explique Pierre-Olivier Salmon, responsable de la communication chez le constructeur PSA Peugeot – Citroën. « En plus, nous faisons circuler des questionnaires parmi les effectifs afin d’identifier nos faiblesses. » Par ailleurs, des « Fiches de Postes » qui décrivent la fonction associée à chaque poste de travail dans l’usine, sont mises à la disposition des employés. L’Institut national de recherche et sécurité (INRS) recommande d’y intégrer des informations sur les risques encourus.
Maux persistants
Malgré tout, chez les ouvriers, douleurs, lumbago et troubles musculosquelettiques (TMS) tendent à se multiplier au niveau des bras (224 salariés touchés en 2010), des mains (263), des jambes (265) et du dos (298). A en croire les syndicats, le problème touche particulièrement les intérimaires du secteur automobile. Lesquels n’apparaissent pas dans les statistiques de la CNAMTS… « Employés massivement par les constructeurs, ils peuvent représenter jusqu’à 70 % des effectifs au travail sur la ligne de production », glisse Fabien Gâche, délégué central CGT du groupe Renault. « Parfois, ils sont encouragés à ne pas déclarer leurs accidents de travail. En échange, ils obtiennent la promesse d’être rappelé lors des missions suivantes… » Parmi les autres salariés concernés par le risque mécanique dans la construction automobile, il ne faut pas oublier les équipementiers qui fabriquent les pièces détachées. Sont particulièrement visés ceux qui produisent les pièces mécaniques, telles que les moteurs.
Le risque mécanique chez les équipementiers automobiles
Dans l’industrie automobile, certaines pièces sont fabriquées sur d’autres sites de production et livrées à l’usine au moment exact où elles doivent être installées. C’est le cas, par exemple, des selleries ou des revêtements de sol mais également des pièces mécaniques telles que les moteurs et les boîtes de vitesse. Issus de l’industrie métallurgique, la fabrication de ces derniers éléments nécessite pour les salariés de s’équiper d’équipements de protection individuelle (EPI) particuliers. Par exemple, des gants, des écrans faciaux et des combinaisons thermiques pour se protéger des projections de liquides brûlants. Mais également des lunettes de protection infrarouges afin de se prémunir contre les rayonnements caractéristiques du métal en fusion.
Glissades fatales
Il s’agit d’un dilemme pour les constructeurs : comment augmenter les cadences et gagner en productivité sans décupler les risques mécaniques pour les employés ? « Les temps morts durent moins d’une seconde », lâche le délégué de la CGT. « Pour les travailleurs, ce sont autant de moments de répit en moins. » Entre autres conséquences de ces cadences infernales, les glissades, trébuchements, faux pas et autre pertes d’équilibre sur des sols glissants, car mal nettoyés, sont monnaie courante dans les usines de construction automobile. En 2010, 363 personnes en ont fait les frais, avec des conséquences allant de la simple contusion, aux entorses, plaies et fractures les plus graves. Plus grave, pour 37 d’entre eux, l’expérience s’est soldée par une incapacité permanente de travail.
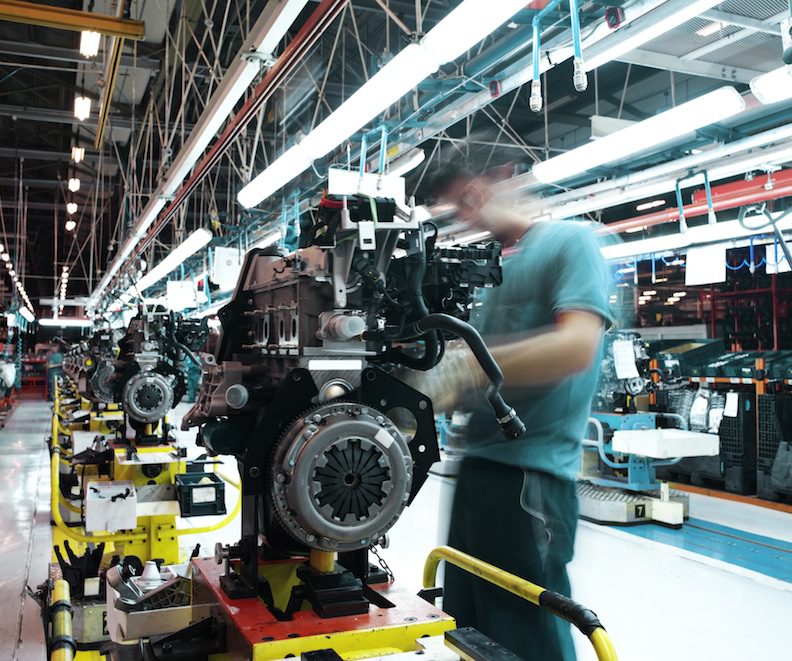
Facteurs aggravants
Anodin en apparence, ce type d’accident peut s’aggraver, même si le salarié ne chute pas. En effet, le risque résulte d’une combinaison de différents facteurs. Comme par exemple, la présence d’un objet brûlant à proximité et sur lequel le salarié se rattrape.
« Pour pallier ce risque, il faut distribuer aux employés des gants de protection et surveiller qu’ils les portent », souligne Christine Breton, médecin à la Caisse régionale d’assurance maladie d’Ile-de-France (CRAMIF). Le responsable sécurité doit également organiser l’usine de manière à anticiper le risque de chute. Il peut, par exemple, sécuriser les fosses qu’utilisent les techniciens pour travailler sous les véhicules. Il faut notamment veiller à les recouvrir lorsqu’elles ne sont pas en service ou les signaler dans le cas contraire.
Contusions nombreuses
Parmi les différents types de lésions recensées par l’assurance maladie (fractures, fêlures, coupures, entorses, luxations…), les contusions tiennent le haut du pavé. Ce type de douleurs, à l’origine de 50 déclarations d’incapacité permanente en 2010, guette particulièrement les salariés qui manipulent des charges lourdes (473 accidents) et ceux qui les transportent (69 accidents). Sont aussi concernés les salariés qui travaillent à proximité de pièces contondantes : la CNAMTS relève 36 cas d’accidents de travail survenus à cause de mouvements accidentels d’objets. Parmi les postes vulnérables, citons les ouvriers qui travaillent au début de la ligne de production, dans l’atelier d’emboutissage. Ils découpent les tôles livrées en rouleau et les déposent – étape délicate – sur un tapis roulant, qui les conduit à la presse. Cette machine leur donne ensuite la forme des différentes parties du véhicule (portières, planchers, ailes…) via un procédé de moulage.
Le bruit, un risque coûteux
Le bruit est omniprésent dans les usines de construction automobile… voire assourdissant. « Au dessus de 80 décibels pendant huit heures, l’employeur doit fournir des EPI à ses salariés », souligne Jacques Châtillon, chef du laboratoire d’acoustique à l’Institut national de recherche et sécurité (INRS) de Nancy, en Meurthe-et-Moselle (54). « Au dessus de 85 décibels l’employeur a l’obligation de vérifier que ces protections sont portées. » En outre, des protections collectives doivent être installées, comme par exemple des « encoffrements » autour des machines, à savoir des caissons isolants constitués de tôles assez dures pour arrêter le bruit et de mousse pour l’absorber. Enfin, il existe des « silencieux » (à l’instar des revolvers) qui se fixent au bout des échappements pneumatiques de certaines machines, ainsi que des lames silencieuses pour les engins coupants. Autre possibilité : le recours à un plafond acoustique.
Outre le risque sanitaire, la problématique est également financière. « En moyenne, la perte d’audition d’un seul salarié coûte 100 000 euros à l’assurance maladie. »
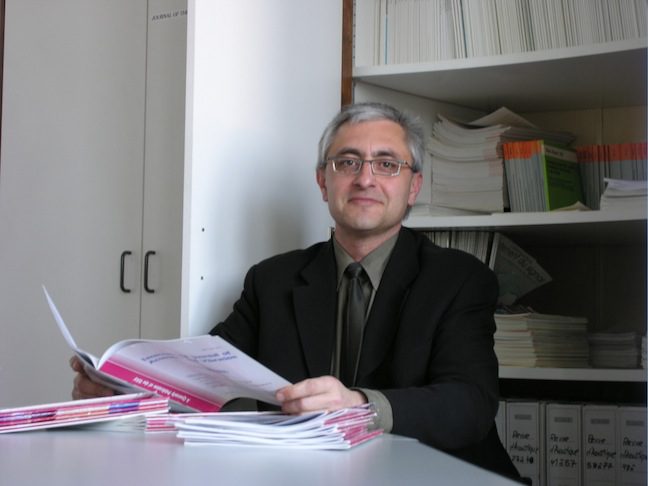
Port de charges
La loi interdit aux travailleurs de porter ces tôles manuellement et, d’une manière générale, de transporter, de façon habituelle, des charges supérieures à 55 kg sans l’accord préalable du médecin du travail (article 4541-9 du code du travail). Elle impose également aux dirigeants de mettre des aides mécaniques à disposition des salariés (article R 4541-5 du code du travail). Il peut s’agir par exemple de palans, à savoir un système de poulie qui réduit l’effort de portage. « Mais ces équipements peuvent tomber en panne », insiste Fabien Gâche. « Dans ce cas, il n’est pas rare que le salarié porte lui-même, manuellement, la tôle découpée jusqu’à la presse afin de ne pas ralentir la ligne de production… » Une dérive organisationnelle qui est à l’origine de plusieurs problèmes de santé, tels que des fissures (ou des ruptures) du ménisque, un élément cartilagineux situé au niveau du genou, ainsi que des tendinites, des douleurs dorsolombaires et des sciatiques.
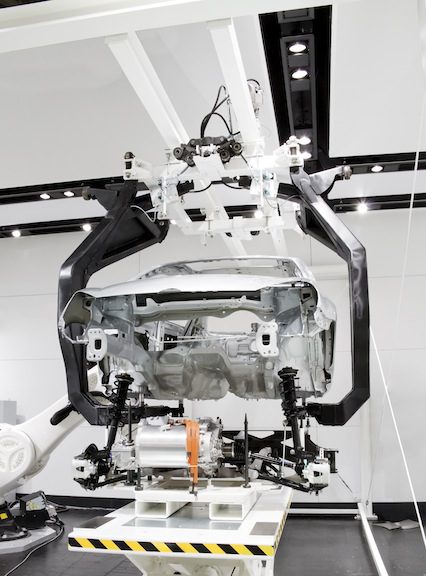
Lames de rasoir
Une fois « pressées », les tôles découpées sont acheminées, par tapis roulant interposé, vers des salariés chargés de les réceptionner puis de les ranger dans des caisses. Tranchantes comme des rasoirs, ces pièces doivent impérativement être saisies avec des gants, sous peine d’accroître le nombre (déjà important) de salariés victimes de coupures dans le secteur de la construction automobile. A savoir, 151 personnes en 2010, selon les chiffres fournis par la CNAMTS. Une fois triées, les pièces sont transportées par un cariste, lequel doit penser à porter les équipements réglementaires liés à sa profession (chaussures de sécurité, casque…). Les tôles sont ensuite déposées sur un autre tapis roulant qui les achemine vers l’atelier de « ferrage ». Là, elles sont soudées les unes aux autres par des robots afin que, petit à petit, se constitue comme un puzzle la carcasse du véhicule.
Projections métalliques
Dans cet atelier très automatisé, des salariés travaillent à proximité des machines. Soit pour contrôler, en amont, le bon déroulement du processus et éventuellement intervenir afin d’assurer des opérations de maintenance. Soit pour vérifier, en aval, la présence de défauts sur la carrosserie et les corriger par ponçage et polissage. « Ces opérations génèrent des projections de particules métalliques », explique Christine Breton. « Afin d’éviter que ces dernières n’atteignent les yeux du travailleur, il faut s’équiper de ponceuses munies d’un système d’aspiration intégré et travailler au-dessus d’un plancher aspirant. Il faut également distribuer aux salariés des lunettes de protection. » En outre, pour se protéger dans cet environnement particulièrement assourdissant, il convient d’ajouter des bouchons d’oreilles ou des casques antibruit.

Postures et tremblements
Les salariés qui travaillent au ponçage des véhicules sont particulièrement vulnérables aux TMS. En cause, notamment, la vibration des outils. « Il faut privilégier l’achat d’outillage disposant d’un niveau vibratoire bas », reprend le médecin de la CRAMIF. Une donnée inscrite sur l’étiquette de l’appareil… Mais le risque zéro n’existe pas. « Les niveaux de vibrations restent élevés, même lorsque les engins respectent la norme fixée par la directive européenne 2002/44/CE… » Pour minimiser l’apparition de TMS chez le travailleur, il convient donc d’actionner d’autres leviers. Par exemple, en choisissant les outils et machines en fonction de leur ergonomie.
« L’effet recherché, c’est de limiter les mauvaises postures des utilisateurs », explique Pierre-Olivier Salmon. En outre, les actions de chaque salarié doivent être décortiquées par la direction chargée des risques pour la santé, afin d’identifier et réformer certaines situations de travail. Particulièrement celles où le travailleur doit travailler les bras en l’air. Idem pour celles qui impliquent des mouvements répétés du poignet.
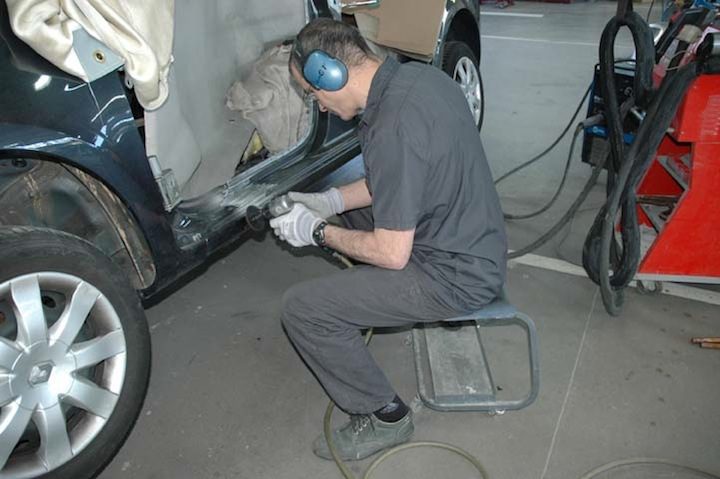
Robots « tueurs »
Après les phases d’emboutissage et de ferrage arrivent les phases de peinture de la carrosserie, puis de montage des pièces détachées livrées par les équipementiers. En pratique, il s’agit des dernières étapes avant le contrôle technique puis le stockage du véhicule en attendant sa livraison au concessionnaire du constructeur. A tous les stades, le parcours est jalonné de robots qui peuvent constituer une menace pour les salariés. Particulièrement pour ceux qui sont chargés de leur maintenance. En pratique, le risque porte sur des aléas réguliers. « Par exemple un bourrage ou un produit à recharger », souligne Elodie Falconnet, responsable de l’activité sécurité des machines, au Centre technique des industries mécaniques (CETIM).
« Avant d’intervenir, il faut vérifier que la machine est sûre [désactivée NDLR]. » Le risque (mortel) : que le robot se mette en marche et écrase l’opérateur. Causant alors la mort pure et simple du salarié.
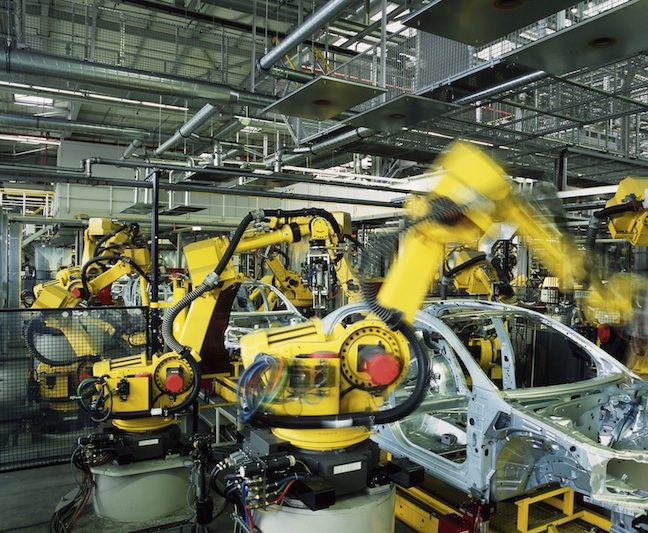
Protections contre les machines
Le responsable de la sécurité doit également veiller à protéger tous les salariés, en vérifiant que la machine possède les protections indispensables : verrouillages physiques à l’aide d’un interrupteur sécurisé, circuits de commandes protégés par mot de passe, carters de protection visant à isoler les courroies de l’appareil afin d’éviter que les salariés ne se coincent les doigts à l’intérieur… « Dans certains cas, il faut grillager la périphérie de la machine ou installer des barrières immatérielles [par exemple, un système de détection de présence infrarouge NDLR] tout en se ménageant des points d’accès », explique l’experte du CETIM. Reste à informer les salariés des risques encourus en intégrant dans la Fiche de poste, les règles d’utilisation de la machine.
© Guillaume Pierre, agence TCA-innov24
Commentez