L'industrie fait sa mue numérique en s'appuyant notamment sur une automatisation plus poussée des processus. Dans ce contexte, l'humain a un rôle stratégique à jouer en réalisant des activités à forte valeur ajoutée. Ce qui réclame de veiller à ses conditions de travail en adoptant de nouveaux outils tels que des robots collaboratifs, les lunettes connectées, etc. de manière à réduire la pénibilité physique et mentale du poste de travail.
L’industrie 4.0 est en ordre de marche. Portée par la robotisation des processus, les algorithmes d’intelligence artificielle, la Blockchain et la cybersécurité, cette révolution numérique commence à porter ses fruits en matière de flexibilité et productivité, mais aussi de réduction des coûts et des délais de livraison. Selon le cabinet Mazars, qui s’appuie sur une enquête menée par OpinionWay auprès de 203 dirigeants de grandes entreprises françaises et d’ETI, 80% des sondés sont convaincus de l’intérêt de l’Industrie 4.0 et 95% se déclarent prêts à s’adapter aux changements. Les PMI devraient suivre, sachant que l’État français prévoit d’adopter un nouveau dispositif de suramortissement des investissements consacrés à la robotisation et à la transformation digitale des entreprises. 250 millions d’euros devrait ainsi y être consacrés, ainsi qu’une déduction de 40% du montant des investissement sur deux ans. De quoi donner des ailes à l’industrie du futur. A condition, toutefois, de convaincre les salariés que cette révolution industrielle ne sera pas le triomphe du tout automatique. Le groupe Bosch Rexroth, qui a déployé plus de 150 projets autour de l’usine du futur, en fait le pari. Fort de son expérience, l’industriel a publié en 2018 un livre blanc consacré à l’ergonomie 4.0. Dans ce document d’une dizaine de pages, les entreprises sont invitées à identifier les points clés du processus sur lesquels l’opérateur est susceptible d’intervenir, en apportant de la valeur ajoutée en termes de réactivité et de qualité. Pour que ce scénario porte ses fruits, il est en effet indispensable d’éviter l’apparition de troubles musculosquelettiques (TMS) ou de risques psychosociaux liés à de nouvelles organisations du travail.
Les Wearables pour alléger la charge mentale
Dans ce contexte, les nouvelles technologies digitales sont appelées à améliorer les conditions de travail aussi bien dans les ateliers de production que dans les sites de logistique. A commencer par les casques et lunettes connectés à réalité augmentée. Ces Wearables, à l’instar des lunettes de l’allemand Picavi, affichent dans le champ visuel de l’opérateur des informations pour lui désigner les pièces ou les outils à prendre. Ils peuvent même le guider vers l’endroit où les pièces doivent ensuite être déposées. Pour enlever les écrans des mains de l’opérateur, l’usine et l’entrepôt 4.0 peuvent aussi compter sur les nouvelles interfaces permettant de commander les machines par la voix, le regard ou le geste. Autre piste prometteuse : les systèmes de reconnaissance de l’utilisateur. L’intérêt est d’adapter la hauteur et l’éclairage du poste de travail en fonction des besoins des utilisateurs, qui peuvent ainsi tourner sur un même poste sans avoir à procéder eux-mêmes à de multiples réglages fastidieux. De quoi susciter l’adhésion des salariés et les fidéliser. Ce point est d’autant plus stratégique que les machines sur lesquelles ils travaillent doivent subir des mises à jour régulières, réclamant une formation permanente des salariés.
Des robots collaboratifs pour limiter les risques de TMS
L’arrivée des robots coopératifs et collaboratifs est également vouée à contribuer à l’amélioration des conditions de travail. A la différence des générations précédentes, ces machines sont conçues pour travailler en toute sécurité avec l’homme, dans le même espace de travail. Les robots coopératifs exécutent des tâches complémentaires à celles de l’opérateur. Par exemple, ils vont remplir des bacs ou charger des palettes avec les pièces qui auront été traitées par l’opérateur. Ce qui limite les risques de lombalgies et de TMS liés à la manipulation de charges lourdes. A l’inverse, les robots collaboratifs travaillent main dans la main avec un autre robot qui va, par exemple, porter et manipuler des pièces sur lesquelles intervient simultanément l’opérateur. Ce qui lui évite d’avoir à exécuter des gestes répétitifs. Facteurs de réduction de la pénibilité, les robots coopératifs et collaboratifs sont néanmoins porteurs de nouveaux risques. Par exemple, mal réglés, ils sont susceptibles d’augmenter ou de ralentir la cadence. D’où la nécessité de veiller à leur bon fonctionnement pour ne pas susciter de sentiment d’insécurité chez les opérateurs.
Eliane Kan
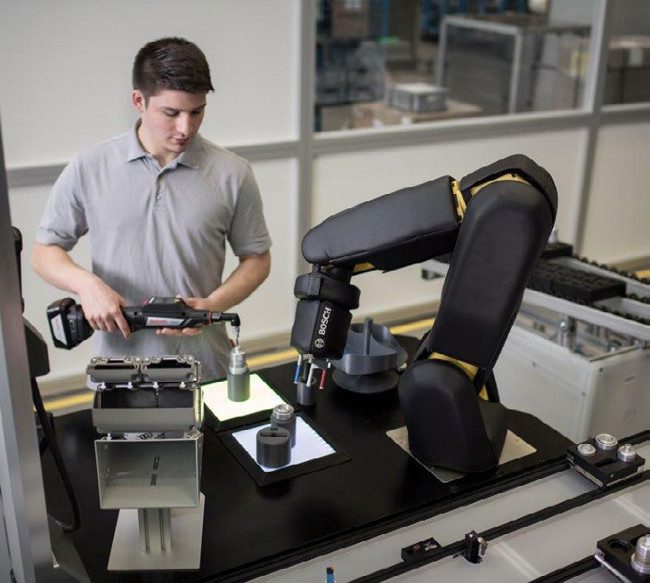
© Bosch Rexroth
Commentez